一、片劑成型原理:
片劑的成型過程(幾種結(jié)合力):
(1)在壓力下顆粒shou先發(fā)生相對(duì)移動(dòng)或滑動(dòng),從而排列的更加合理,然后顆粒被迫發(fā)生塑性或彈性變形,使體積進(jìn)一步變形。
(2)部分顆粒破碎生成大量新的未被污染的顆粒,具有巨大的表面積與表面能,因此表現(xiàn)出較強(qiáng)的結(jié)合力以及靜電作用力,促使顆粒結(jié)合成具有一定孔隙率的片劑。
(3)顆粒受壓后發(fā)生熔融現(xiàn)象,壓力解除后形成“固體橋”。
二、制片的兩個(gè)重要前提條件:
即用于壓片的物料(顆?;蚍勰?應(yīng)具有良好的可壓性與流動(dòng)性。
可壓性是指物料在受壓過程中可塑性的大小,可塑性大即可壓性好,易成型。對(duì)于可壓性不能滿足生產(chǎn)需要的物料,選擇可壓性好的輔料來調(diào)節(jié)或改善原物料的可壓性。良好的流動(dòng)性,可保證片劑的分劑量準(zhǔn)確。
三、影響片劑成型的主要因素:
1.藥物可壓性:(比較物料的塑性與彈性)塑性比較大時(shí)可壓性好,彈性大時(shí)可壓性差。彈性大小用彈性復(fù)原率來表示,即:
彈性復(fù)原率 = (Ht-H0)/H0×100%
H0為加壓狀態(tài)下的片劑的高度,Ht壓力解除后片劑的高度。
2.藥物的熔點(diǎn)及結(jié)晶形態(tài):藥物的熔點(diǎn)低有利于固體橋的形成,即有利于片劑成型。立方晶系對(duì)稱性好,表面積大壓縮易成型。
3.黏合劑與潤滑劑:黏合劑用量大片劑容易成型,但用量過大造成片劑硬度大,使其崩解、溶出困難;疏水性潤滑劑用量過多,使粒子間的結(jié)合力減弱,造成片劑的硬度降低。
4.水分:顆粒中含有適量的水分或結(jié)晶水有利于片劑的成型,但含水量過多會(huì)造成黏沖現(xiàn)象。
5.壓力:一般情況下,壓力增加片劑的硬度會(huì)隨之增大,但當(dāng)壓力超出一定范圍后,壓力對(duì)片劑硬度的影響減小。另外加壓時(shí)間延長有利于片劑的成型。
四、片劑的質(zhì)量問題:
(一)裂片:片劑發(fā)生裂開的現(xiàn)象叫做裂片(常發(fā)生頂裂或腰裂)
產(chǎn)生原因:
片劑的彈性復(fù)原率(與物料性質(zhì)有關(guān))及壓力分布不均勻是主要原因。
另外,粘合劑不當(dāng)或用量不足、細(xì)粉過多、顆粒過干、加壓過快均會(huì)造成裂片。
解決方法:
換用塑性大的輔料,適度干燥,選擇合適粘合劑與用量,減少細(xì)粉等。
(二)松片:指片劑的硬度不夠,稍加觸動(dòng)即散碎的現(xiàn)象稱為松片。
產(chǎn)生原因:
與壓力及粘合劑的用量等諸多因素有關(guān)。
解決方法:
調(diào)整壓力和適當(dāng)增加粘合劑。
(三)粘沖:指片劑表面被沖頭粘去一薄層或一小部分,造成片面粗糙不平或有凹痕的現(xiàn)象。
產(chǎn)生原因:
顆粒不夠干燥或物料易于吸潮、潤滑劑選擇不當(dāng)或用量不足,
以及沖頭表面銹蝕或刻字粗糙不光等。
解決方法:
應(yīng)根據(jù)實(shí)際情況而定。
(四)片重差異超限:片劑的重量超出藥典規(guī)定的重量差異允許的范圍。
產(chǎn)生原因:
粒的流動(dòng)性不好;
細(xì)粉過多或顆粒不均勻;
加料斗內(nèi)物料時(shí)多時(shí)少;
沖頭與??孜呛喜缓?。
解決方法:
改善物料流動(dòng)性等。
(五)崩解遲緩:指片劑不能在藥典規(guī)定的時(shí)限內(nèi)完全崩解或溶解
1.崩解機(jī)理
(1)片劑中可溶性成分多,因溶蝕而崩解;
(2)“固體橋”溶解,結(jié)合力消失;
(3)泡騰劑產(chǎn)氣作用;
(4)吸水膨脹(多數(shù)片劑)。
(5)潤濕熱
2.影響崩解的因素
毛細(xì)管理論公式:L2 = Rγcosθ/2η.t
式中L:液體滲入毛細(xì)管的距離;R:毛細(xì)管半徑;γ:液體的表面張力;θ:液體與毛細(xì)管的接觸角;η:液體的黏度,t:時(shí)間。由公式可知,影響介質(zhì)滲入的主要參數(shù)有:毛細(xì)管數(shù)量(孔隙率)、毛細(xì)管半徑、液體表面張力與接觸角。
產(chǎn)生影響的主要因素是以下幾方面:
(1)原輔料的可壓性:原輔料的可壓性好,片劑的崩解性能差,適量加入淀粉可增大片劑的空隙率,增加吸水性,有利于片劑的崩解;
(2)顆粒的硬度:顆粒的硬度小影響片劑的孔隙率,近而影響片劑的崩解;
(3)壓片力:壓力大,片劑的孔隙率及孔隙徑小,片劑崩解速度慢;
(4)表面活性劑:加入表面活性劑,改變物料的疏水性,增加潤濕性,有利于片劑的崩解;
(5)潤滑劑:使用疏水性強(qiáng)的潤滑劑,水分不易進(jìn)入片劑,不利于片劑的崩解,硬脂酸鎂;
(6)粘合劑與崩解劑:粘合力越大,崩解時(shí)間越長,黏合劑粘合力大小順序:明膠>阿拉伯膠>糖漿>淀粉漿。
(7)崩解劑:見崩解劑部分。
(8)貯存條件:貯存環(huán)境的溫度與濕度影響片劑的崩解。
(六)溶出超限:片劑在規(guī)定的時(shí)間內(nèi)未能溶出規(guī)定量的藥物,即為溶出超限或稱為溶出度不合格。
溶出理論:溶出服從Noyes-Whitney方程:dc/dt=kSCs
dc/dt為溶出速度;k為溶出速度常數(shù);s為溶出質(zhì)點(diǎn)暴露于介質(zhì)的表面積;cs為藥物的溶解度。
由公式說明,產(chǎn)生溶出超限的原因是:崩解遲緩;藥物難溶。
解決方法:
(1)物微粉化:s值增大;
(2)制備研磨混合物:疏水性藥物與水溶性或親水性材料研磨混合,改變藥物的潤濕性;
(3)制成固體分散體:改變藥物的粉散狀態(tài),s值增大,有利于藥物的溶出;
(4)吸附于載體后壓片:藥物以分子態(tài)形式被吸附在載體表面,有利于溶出。
(七)片劑含量不均勻
所有造成片重差異過大的因素,均可造成片劑中藥物含量不均勻,此外小劑量片藥物含量不均勻的主要原因是:#p#分頁標(biāo)題#e#
1.混合不均勻
(1)主藥與輔料量的配比懸殊:
(2)主藥與輔料粒子大小相差懸殊:
(3)粒子的表面粗糙不易混勻:
(4)由于顆粒大小不等而對(duì)藥液的吸收量不同。
2.可溶性成分在干燥過程中的遷移
五、片劑的質(zhì)量檢查: (一)外觀
(二)片重差異
重量差異限度與評(píng)價(jià)標(biāo)準(zhǔn):
標(biāo)準(zhǔn):超過限度的片不得多于2片,且1片不得超出限度1倍。糖衣片、薄膜衣片應(yīng)在包衣前檢查片心重量差異。
(三)脆碎度
用Roche
脆碎度測(cè)定儀,通常脆碎度<1%為合格。
(四)崩解度
1.咀嚼片、緩、控釋片,不需要作崩解時(shí)限檢查。
2.標(biāo)準(zhǔn):
普通壓制片:應(yīng)在15min內(nèi)全部崩解
薄膜衣片:應(yīng)在30min內(nèi)全部崩解
糖衣片:應(yīng)在60min內(nèi)全部崩解
腸衣片:先在鹽酸溶液(9→100)中檢查2h,每片不得有裂縫崩解或軟化現(xiàn)象,于pH為6.8的磷酸鹽緩沖液中1h內(nèi)應(yīng)全部崩解。
含片:應(yīng)在30min內(nèi)全部崩解或溶化。
舌下片:應(yīng)在5min內(nèi)全部崩解或溶化。
可溶片:水溫15℃~25℃,應(yīng)在3min內(nèi)全部崩解或溶化。
結(jié)腸定位腸溶片:pH為7.8~8.0的磷酸鹽緩沖液中60min內(nèi)全部釋放或崩解。
(五)溶出度或釋放度檢查
1.溶出度:是指藥物從片劑或膠囊等固體制劑在規(guī)定的介質(zhì)中溶出的速度和程度。凡檢查溶出度或釋放度的制劑,不在進(jìn)行崩解時(shí)限的檢查。
2.要求作溶出度檢查的片劑:
(1)含有在消化液中難溶的藥物片劑;
(2)與其他成分容易發(fā)生相互作用的藥物片劑;
(3)久貯后溶解度降低的藥物片劑;
(4)劑量小,藥效強(qiáng),副作用大的藥物片劑。
3.藥物的溶出度可以反應(yīng)藥物在體內(nèi)吸收的情況,藥物體外溶出與體內(nèi)吸收具有相關(guān)性。
(六)含量均勻度檢查
含量均勻度:是指小劑量或單劑量固體制劑、半固體制劑和液體制劑的每片(個(gè))含量符合標(biāo)示量的程度。
需進(jìn)行含量均勻度檢查的制劑:
1.片劑、膠囊劑或注射用無菌粉末,每片(個(gè))標(biāo)示量小于10mg或主藥含量小于每片重量的5%者。
2.其他制劑,每個(gè)標(biāo)示量小于2mg或主藥含量小于每個(gè)重量的2%者,以及透皮貼劑均應(yīng)檢查均勻度。
3.藥物的有效濃度與毒副反應(yīng)濃度比較接近的品種或混勻工藝?yán)щy的品種,每片(個(gè))標(biāo)示量不大于25mg,也應(yīng)檢查均勻度。
4.復(fù)方制劑僅檢查符合上述條件的組分。
凡進(jìn)行含量均勻度檢查的制劑,不再進(jìn)行重(裝)量差異的檢查。
六、常用粘合劑:
某些藥物粉末本身具有黏性,加入適當(dāng)?shù)囊后w(多為乙醇水溶液)能誘發(fā)待制粒物料的粘性以利于制粒的液體,被稱為潤濕劑;某些藥物粉末本身無粘性或粘性較小,需加入淀粉漿等黏性物質(zhì),才能使其黏合起來,加入的黏性物質(zhì)稱為黏合劑。它們的作用都是使粉末黏合起來,故總稱為黏合劑。
常用粘合劑
種類 主要性能特點(diǎn)
是一種潤濕劑,干燥溫度高,且
蒸餾水 易被物料吸收,發(fā)生潤濕不均勻
現(xiàn)象,不適宜單獨(dú)使用
是一種潤濕劑,乙醇濃度增大,
乙醇 潤濕后產(chǎn)生的粘性降低,中藥浸
膏片常用乙醇作潤濕劑 應(yīng)用 同淀粉(淀粉漿)及乙醇合用,不適于對(duì)水敏感的藥物。 適用于遇水易分解或遇水粘性太大的藥物。常用30~70%濃度乙醇
淀粉在水中受熱糊化而得,玉米
淀粉漿
淀粉的完全糊化溫度為77℃。
**常用的粘合劑和潤濕劑,常用濃度8%~15%,
可用沖漿法(多)和煮漿法制得,**常用濃度為10%,濃度不宜直火加熱。
纖維素的羧甲基醚化物的鈉鹽,
視物料性質(zhì)而定。
羧甲基纖維素鈉(CMC-Na)
溶于水,不溶于乙醇。**好在初步膨化與溶脹時(shí)加熱60~70℃。黏性較強(qiáng),注意制得片劑硬度過大或崩解超時(shí)限。
常用于可壓性較差的藥物
羥丙纖維素HPC
纖維素的羥丙基醚化物,易溶于冷水,加熱**50℃發(fā)生膠化或溶脹現(xiàn)象
既可作濕法制粒的粘合劑,也可作粉末直接壓片的干粘合劑
應(yīng)用于水溶性及水不溶
甲基纖維素 MC
纖維素的甲基醚化物,水溶性好,形成粘性膠體溶液
性物料的制粒中,形成的顆粒壓縮成型性好,不隨時(shí)間變硬
纖維素的甲基醚化物,不溶于水,在乙醇等有機(jī)溶媒中溶解度
乙基纖維素EC
較大,用作對(duì)水敏感的藥物的黏合劑,對(duì)片劑的崩解及藥物釋放起阻滯作用。
羥丙甲纖維素HPMC
纖維素的羥丙甲基醚化物,易溶于冷水,不溶于熱水,崩解速度快,溶出快。
常用濃度2~5%,比較新型的粘合劑,作干粘合劑(直接壓片)
用于緩、控釋制劑的制備
其他黏合劑:5%~20%的明膠溶液;50%~70%的蔗糖溶液;3%~5%的PVP溶液。 沖漿法:淀粉+1-1.5倍冷水→攪勻→沖入全量沸水**半透明糊狀(常用于大生產(chǎn)、方便)
煮漿法:淀粉+全量冷水→蒸汽加熱→糊化(少用) 七、常用崩解劑:
崩解劑:是使片劑在胃液中迅速裂碎成細(xì)小顆粒的物質(zhì)。
常用崩解劑 種類
主要性能特點(diǎn)
應(yīng)用
應(yīng)用**廣泛、**
干淀粉
吸水性較強(qiáng)且有一定的膨脹性,較適用于水不溶性或微溶性藥物的片劑。在生產(chǎn)中一般采用外加法、內(nèi)加法或內(nèi)外加法作崩解劑。
經(jīng)典的崩解劑,一般用量為干顆粒的5~20%
羧甲基 淀粉鈉CMS-Na 低取代羥丙基纖維素L-HPC 交聯(lián)聚維酮PVPP 交聯(lián)羧甲基纖 維素鈉CCNa 泡騰 崩解劑#p#分頁標(biāo)題#e#
是一種特殊的崩解劑**常用的是碳酸氫鈉與枸櫞酸組成的混合物。生產(chǎn)與貯存過程中妥善包裝,嚴(yán)格防水
用于泡騰片劑
于水中不溶解,能吸收數(shù)倍自身重量的水,而膨脹,具有較好的崩解作用。 與干淀粉合用崩解作用降低。
與羧甲基淀粉納合用崩解效果更好。
在水、有機(jī)溶劑及強(qiáng)酸強(qiáng)堿中均不溶,于水中迅速溶脹,并且不會(huì)出現(xiàn)高黏度凝膠層,崩解性能十分優(yōu)越。而不溶解崩解效果好,但引濕性很強(qiáng)
優(yōu)良崩解劑
具有很大的表面積和空隙度,所以具有很好的吸水速度與吸水量,吸水膨脹率為500%~700%
本品作崩解劑用量為2~5% 是一個(gè)性能優(yōu)
于水中吸水膨脹性非常顯著,為原體積的300倍。 良的崩解劑。用
量為片重的1~6%
八、常用潤滑劑:常用潤滑劑 種類
主要性能特點(diǎn)
疏水性潤滑劑,附著性好,潤滑
硬脂酸鎂
作用好,用量大時(shí)片劑不易崩解或裂片。與乙酰水楊酸、某些抗生素及多數(shù)有機(jī)堿不能配伍。 可減低顆粒表面的粗糙性物料對(duì)
滑石粉
沖頭的粘附性,以達(dá)到降低顆粒間的摩擦力,改善顆粒的流動(dòng)性。
微粉硅膠 氫化植物油 聚乙二醇4000和6000 月桂醇硫酸鎂
水溶性潤滑劑
作助流劑使用常用量0.1~3%
應(yīng)用**廣泛。一般用量0.1~1% 應(yīng)用
為白色輕質(zhì)無水粉末,
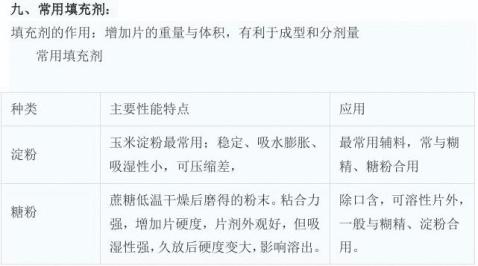
無臭無味,粉末直接壓片的助流比表面積大。
是一種潤滑性能良好的潤滑劑
劑,常用量0.1~0.3% 溶于輕質(zhì)液體石蠟中噴到顆粒上 用于可溶性片劑的制備
淀粉水解的中間產(chǎn)物,沸水中溶成膠
糊精
狀,不溶于乙醇。有較強(qiáng)粘結(jié)性。使用不當(dāng)易出現(xiàn)水印和麻點(diǎn),影響崩解、溶出和主藥的含測(cè)。
由等分子葡萄糖及半乳糖組成,常用
乳糖
含1個(gè)結(jié)晶水的α型,甜味,易溶于水,無吸濕性,可壓性、流動(dòng)性好,性質(zhì)穩(wěn)定,制得片劑外觀好。
可壓性淀粉(預(yù)膠化淀粉)
本品是多功能輔料,具有良好的流動(dòng)性、可壓性、自身潤滑性和干粘合性并有較好的崩解作用。
由纖維素部分水解得到的聚合度較小的結(jié)晶性纖維素,具有較強(qiáng)的結(jié)合力和良好的可壓性,片劑中含20%以上的含量具有較好的崩解作用。 穩(wěn)定,可與多種藥物配伍,所制片外觀光潔,硬度、崩解均好,常使用二水硫酸鈣,與Ca2+反應(yīng)的藥物不能用 口中溶解時(shí)吸熱,有清涼感,兼有一定甜味,咀嚼物無砂礫感。
多用作咀嚼片、口含片填充劑,常與蔗糖配合使用
常使用二水硫酸鈣, 可作粉末直接壓片的干黏合劑使用。 除作填充劑外,常用于直接壓片
除作填充劑外,常用于直接壓片(需加入不超過0.5%硬脂酸鎂)
常與淀粉、糖粉合用
微晶纖維素MCC
無機(jī)鹽類(鈣鹽)
甘露醇
十、片劑常見問題分析: 松片
一、設(shè)備原因 1.一般情況:
1.1下沖打斷,顆粒裝量減少
1.2下沖下得不好:如細(xì)粉太多,或天氣潮濕。細(xì)粉受潮垢住下沖,或油垢等原因造成。
1.3沖模??滋?,大量細(xì)粉漏下,造成垢沖。
1.4壓了重片,特別是上沖變短。
1.5上、下沖未測(cè)量,長短不一。
2.屬于壓力不足造成的:
2.1壓力較小,未壓結(jié)實(shí)。
2.2調(diào)壓器未鎖緊造成松動(dòng),下壓輪下移。
2.3換批后未調(diào)整壓力。
2.4長期未加顆粒,漏斗中顆粒太少。
3.屬于漏斗方面的原因:
3.1漏斗堵塞,顆粒不下,堵塞原因;
3.2有異物:如布片,木片、片子、大塊顆粒等。
3.3顆粒架橋:如顆粒太濕,滑料太少,細(xì)粉太多,粉末壓片等。
3.4漏斗口子太小,不是形成堵塞,就是顆粒下得不好。
3.5漏斗安裝位置不當(dāng),過低或過前等。
4.其它
4.1花盤堵塞,存在異物:如木片、尼龍絲、布絲、片子、油粉團(tuán)、大塊物料等,影響裝量減少造成松片。
4.2開快車壓片,速度過快,顆粒未裝夠。
5.特殊情況
5.1混料
5.2壓輪磨損:上下壓輪由于淬火不良,或未加油,或上沖、下沖個(gè)別損壞,將壓輪磨損一部分: 或斷續(xù)磨損,則壓片部分沖模壓力減小,而造成松片。
二、顆粒
1.制粒
1.1攪拌時(shí)間不足,顆粒不夠結(jié)實(shí)。
1.2顆粒粘合劑不足,粘力太弱
1.3顆粒粘合劑選擇不當(dāng)造成粘力不夠
1.4粘合劑太多,造成攪拌時(shí)間不夠或太短 1.5
1.6篩網(wǎng)過稀或過緊
2.干燥
2.1顆粒太干,彈性較大,一般應(yīng)保持適當(dāng)水分(1-3%)
2.2顆粒中原料的結(jié)晶水失去過多,造成粘力不足。
3.干燥
3.1潤滑劑用量不足,影響顆粒流動(dòng)不好。
3.2潤滑劑未混合均勻
3.3潤滑劑質(zhì)量不高,體重或不夠細(xì)。
4.原料
4.1植物纖維性顆粒,存在彈性,解壓后片子膨脹。
4.2顆粒細(xì)粉太多,如粉末直壓顆粒。
裂片
一、設(shè)備原因
1.沖模
1.1中模長期使用受壓處凹進(jìn)一圈
1.2上沖或下沖卷邊。造成拉脫一邊而裂片。
1.3上下沖長短不一,太長的造成壓力過大而裂片
1.4沖頭位置不直,或模圈略偏,使壓力一邊大,一邊小,特別是活絡(luò)沖頭。#p#分頁標(biāo)題#e#
2.壓力
2.1壓力過大,片子過于結(jié)實(shí)。
2.2片重超過應(yīng)壓片重太多,而壓力未變,造成壓力過大而裂片。
2.3調(diào)壓器未鎖緊,造成壓力變大。
2.4換批后未調(diào)整壓力。
3.其它
3.1轉(zhuǎn)速過快,片劑受壓時(shí)間太短,解壓太快。
3.2特殊情況:轉(zhuǎn)子盤沖??滓蜷L期使用或公差較大,造成中模在抵緊螺絲時(shí)偏向一邊。使壓力一邊大,一邊小。
二、顆粒
1.制粒
1.1顆粒太結(jié)實(shí),太堅(jiān)硬(必須增加壓力以致裂片)
1.2顆粒細(xì)粉過多,未制結(jié)實(shí)
1.3粘合劑不足,攪拌時(shí)間不夠,篩網(wǎng)松緊不合適造成顆粒細(xì)粉太多。
1.4顆粒率過高,沒有或細(xì)粉太少。
2.干燥
2.1顆粒烘的太干,水分不足造成裂片。
2.2顆粒水分過高,因而粘沖引起裂片或造成腰裂。
3.配料
3.1顆粒過粗過細(xì)等原因,造成填充在??變?nèi)的容量過分不均勻。
3.2顆粒中油類物料太多,或混合不均勻,減少了顆粒間的粘合力。粘力小,就加大壓力造成裂片。
4.原料
4.1富于彈性的物料與纖維性藥物例如酵母或植物性藥物,本身彈性較強(qiáng),解壓后體積膨脹而裂片。
4.2藥物本身的原因,如非那西汀、谷氨酸等藥物晶體,粘性極弱,必須破碎晶體,才可能避免裂片。
4.3潤滑劑過多,反而會(huì)影響裂片,如硬脂酸鎂不可超過1%以上。
4.4個(gè)別藥品如鈣克斯片,硬脂酸鎂超過0。5%以上反而裂隙片。 粘沖
一、設(shè)備原因
1.一般
1.1沖頭使用已久,或保管不善,或沖頭生銹。
1.2沖頭揩拭不徹底,不完全干凈,清潔。
1.3沖頭有卷邊,或破裂。
1.4沖頭刻字太深,筆劃未成圓鈍形具有棱角。
1.5沖頭凹度太深了,在頂部容易粘沖。
2.壓力
2.1壓力不足,造成粘沖。
2.2調(diào)壓器未鎖緊。
2.3換批后未調(diào)整壓力。
3.其它:
3.1天氣潮濕。表面有少量水分附著。
3.2冷設(shè)備剛開車時(shí)容易粘沖,時(shí)間打久了,設(shè)備熱了,粘沖消失。
3.3室內(nèi)相對(duì)濕度太高,應(yīng)降低在60%以下。
二、顆粒
1.制粒
1.1顆粒水分未烘干,或部分干,部分濕,特別是沸騰連續(xù)干燥,容易造成干濕不均。
1.2沸騰床抽力較大,旋風(fēng)分離器與布袋除塵器中回收細(xì)粉沒有烘干。
2.干燥
2.1顆粒太濕,沒有烘干,水分超過規(guī)定。
2.2干燥溫度驟然升高,使顆粒內(nèi)濕外干。
2.3干燥溫度過高藥品分解或溶化因而造成粘沖,如阿司匹林、APC。混合制粒時(shí)AP共熔。
3.配料
3.1顆粒混合不均勻,干濕不均。
3.2顆粒潤滑劑量不足,或選擇不適當(dāng)。
3.3顆粒吸潮,如沒有裝膠口袋(特別是雨天)。
3.4顆粒放置太久,吸了潮,水分超標(biāo)。
4.原料
4.1藥物本身性質(zhì):如柳酸鈉片只能用糊精,不能用淀粉,否則粘沖。
4.2個(gè)別片劑,如含鹽清涼片加入酒石酸在相對(duì)濕度75%時(shí)壓片無問題,若改為枸櫞酸則粘沖嚴(yán)重。
4.3個(gè)別片劑如敵百蟲,受壓時(shí)即溶化而粘沖,又如紅古豆醇酯片也有如此情況。
缺角
一、設(shè)備原因
1.一般
1.1中模有部分損壞
1.2上下沖與中模不配合,打出飛邊。經(jīng)振搖后產(chǎn)生缺角。
1.3上或下沖因故損壞,壓出片子突出一塊。雖不缺角,但也屬完整度不好類型。
1.4花盤擋片板安裝不當(dāng),偏高了,將片子咬缺;
1.5花盤安裝不當(dāng),移前了,片子還沒有完全推出來而撞缺。
1.6下沖升降調(diào)整未調(diào)整好,下沖過低,出片時(shí)撞缺了。
2.其他
2.1用大桶直接接片,片子下落距離過高。
2.2如片子下沖粘沖嚴(yán)重,也易缺角。
二、顆粒
1.一般
1.1顆粒制得不好,如粘合劑不足,淀粉糊不熟,以及攪拌時(shí)間不夠。
1.2顆粒過于堅(jiān)硬,壓出的片子易碎而缺角。
2.原料
2.1生藥纖維彈性較大,如處理不當(dāng),則壓制片后往往經(jīng)不起振搖而缺角。
2.2藥物本身系晶體,特別是鱗片狀晶體,由于晶體表面光滑,降低其粘合能力,即可壓性較差,例如非那西汀如不破壞,極易缺角。
毛邊
一、設(shè)備原因
1.一般
二、顆粒
1.一般情況
1.1顆粒在烘干過程中未烘干,水分較多。
1.2顆粒在存放過程中受潮。
1.3顆粒潤滑劑用量太少。
1.4潤滑劑選擇不當(dāng)如采用硬脂酸鎂的效果就比滑石粉好。
1.5植物纖維性藥材,如中草藥藥片富有彈性,壓出片子易產(chǎn)生毛邊現(xiàn)象。 1.648%以上就產(chǎn)生毛邊。
2.特殊情況
2.1潤滑劑本身質(zhì)量不合格,硬脂酸鎂未打粉過篩,造成潤滑不良而成毛邊。 2.2個(gè)別產(chǎn)品如杜米芬喉片不能采用硬脂酸鎂作潤滑劑,否則失效。采用其他潤滑劑如不胺當(dāng)易易造成毛邊。
飛邊
一、設(shè)備原因
二、顆粒
1.顆粒過濕未烘干,水分超過規(guī)定。
2.顆粒吸潮,被擠壓,而成飛邊。
3.空氣濕度太大,使顆粒細(xì)粉迅速吸濕而被擠壓,形成飛邊。
4.整粒時(shí)加入揮發(fā)油較多,或采用吸油劑不當(dāng),或混合不夠均勻,使顆粒受壓時(shí),易被擠壓而成飛邊。
不崩解
一、設(shè)備原因
二、顆粒
1.制粒
1.1粘合劑粘性太強(qiáng),或選擇不當(dāng)。
1.2粘合劑用量過多#p#分頁標(biāo)題#e#
1.3攪拌時(shí)間太長,顆粒硬度過大
1.4內(nèi)崩解劑用量太少或不足。
2.干燥
2.1干燥溫度過高干燥時(shí)間過長影響顆粒過干,過硬,造成加大壓力,從而影響崩解
2.2顆粒干燥不充分或不夠時(shí)間,造成粘性太強(qiáng)。
3.配料
3.1外崩解劑用量不足或不用造成崩解不良。
3.2崩解劑未混合均勻,造成部分片子不崩解。
3.3崩解劑不完全干燥,吸水力不強(qiáng)。如淀粉不干。
4.原料
4.1主料本身粘性太強(qiáng),崩解選擇不當(dāng),如四環(huán)素。
4.2部分顆粒干燥溫度過高面熔融,造成崩解不好,如阿司匹林
4.3部分原料含有結(jié)晶水,如溫度過高,烤掉結(jié)晶水就影響崩解。如SG片。
4.4疏水性潤滑劑用量過多,過大就會(huì)影響崩解,如硬脂酸鎂用量不能過多。
5.特殊情況
5.1粘合劑糊精質(zhì)量因故變化,如轉(zhuǎn)化率升高合粘性增強(qiáng),造成大批顆粒崩解不合格,如轉(zhuǎn)化率不夠粘性減弱,則造成大批顆粒松片。
5.2個(gè)別產(chǎn)品在沸騰床制粒干燥,由于顆粒比烘箱結(jié)實(shí),壓片時(shí)不注意即崩解不合格,如SM2、SMP片,曾出現(xiàn)如此情況。
重申差異不合格
一、設(shè)備原因
1.沖頭
1.1下沖長短不一,打出片子有輕有重
1.2下訓(xùn)因故下得不好,裝量減少
1.3重量調(diào)節(jié)器設(shè)計(jì)不善
2.壓力
2.1加顆粒時(shí)未經(jīng)常保持漏斗裝滿,未保持一定壓力,造成填充有緊有松。
2.2長期不加顆粒,加粒時(shí)又加太滿。
3.漏斗,花盤
3.1漏斗打空,壓力減少,填充度減少,**后顆粒越來越少。
3.2花盤堵塞,或漏斗顆粒架橋。
3.3雙軌道片機(jī),這邊堵了,那邊沒有堵。
3.4打0。5G左右大片時(shí),車速過快,中模未裝滿。
3.5設(shè)備本身問題,如老式33型壓片機(jī)片子極易跳入花盤。
4.其他
4.1換批后未調(diào)整壓力,且分批不清。
4.2三班片重掌握不一致。
二、顆粒
1.一般
1.1同批顆粒粗、細(xì)相差大,細(xì)粉多片重,細(xì)粉少片輕。
1.2潤滑劑用量不足或混合不均,造成顆粒流動(dòng)性差,時(shí)而流量大,時(shí)而流量小/
1.3顆粒干濕掌握不好,混合不勻。
1.4顆粒細(xì)粉太多,受振動(dòng)分層。
2.特殊
2.1采用粉末直接壓片的顆粒,比重較輕,流量不好。
2.2整粒時(shí)摻入顆?;驓埛圻^多。摻入吸塵器細(xì)粉過多,或集中于小部分顆粒。
2.3某些片劑系分別制粒,臨壓前混合,由于兩種顆粒比重不同,極易分離造成重差,如SD、蘇打片、ST蘇打片、山道年甘汞片。
花斑
一、設(shè)備原因
1. 一般情況
1.1漏斗與轉(zhuǎn)子盤接觸處,因油與粉末積存,變成油粉團(tuán),掉入花盤中造成花斑。
1.2連續(xù)調(diào)速的皮帶輪將三角皮帶夾壞或
二、顆粒
1.制粒
1.1制有色顆粒時(shí),未混合均勻,特別是染色顆粒,如乙胺嘧啶稍不小心,就產(chǎn)生色斑。
1. 2烘布太臟,未洗干凈,或誤用其他產(chǎn)品烘布或烘紙
2.干燥
2.1干燥溫度太高,將產(chǎn)品 烘黃,如VB1粒,氨苯粒等。
2. 2盛粒桶裝過有色顆粒
2.3烘布印有紅色油漆字樣。
3. 整粒
3.1顆粒內(nèi)有異物,如木屑等未挑出
3.2用裝過有色顆粒的桶來裝白色顆粒
3.3加芳香油不遵守規(guī)程,直接倒入,或未加均勻,造成油浸暗斑。
3.4個(gè)別產(chǎn)品如鈣素母片中有骨化醇怕光,如加入不均或見強(qiáng)光引起變色。產(chǎn)生色斑。
4.特殊情況
4.1顆粒整粒后,久置未壓片,或因故長期不能壓片,堆放在顆粒中間站,日久外袋有灰塵或有有色灰塵。
4.2個(gè)別原料個(gè)別包裝單件,因故變色,特別是上面白,下面變色,投料時(shí)倒入混合機(jī)中,引起顏色深淺不一,造成花斑,如安乃近原料曾出現(xiàn)過如此情況
4.3個(gè)別包裝單件變色,同上引起花斑,如四環(huán)素、SM2
色澤不均勻
一、設(shè)備
二、顆粒質(zhì)量
1.制粒
1.1軟材過濕和不均勻
1.2淀粉糊面上結(jié)一層厚皮(HPMC具有成膜性,熱漿,冷漿要結(jié)皮)
1.3軟材過濕,過篩時(shí)成長條,兩頭擠出長條與大塊,干后成僵粒與僵塊
1.4染色片劑如乙胺嘧啶與疳積糖等,如制軟材時(shí)混合不均勻,易產(chǎn)生色澤不均勻或色斑。
1.5顆粒過硬,過多,或細(xì)粉過少,過多以及顆粒之間松散,緊密相差過大等。
2.干燥
2.1沸騰干燥床,制粒有的愛熱熔化變色,但不嚴(yán)重,有的受熱分解變色,如去痛片、APC
3.原料
3.1阿斯匹林晶體直接壓片,產(chǎn)生陰斑
3.2APC片半制粒,阿斯匹林晶體直壓,產(chǎn)生陰斑
3.3非晶體原料如四環(huán)素堿,因批號(hào)不同,顏色深淺就不同,而且相差很大,極易色澤不均。
3.4個(gè)別原料,系母液處理回收產(chǎn)品,顏色較深,投料時(shí)如不注意混在一起,即色澤不均。安乃近原料曾出現(xiàn)此情況。 3.5
3.6晶體直壓,由于結(jié)晶大小不一致壓出片子就產(chǎn)生陰斑,色澤不均勻。
3.7有色藥片加入滑料混合不易均勻,即色澤不勻。
3.8加入揮發(fā)油混合不均,產(chǎn)生小油浸點(diǎn)
3.9復(fù)方片劑,一個(gè)粒硬,一個(gè)粒松,如SD 蘇打片等。